Clean Room Solutions for Pharmaceutical and Industrial Applications:
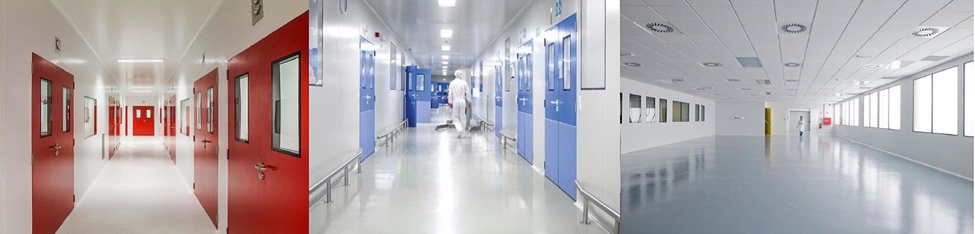
At “Systems BD”, we specialize in providing state-of-the-art clean room solutions tailored to meet the stringent requirements of the pharmaceutical and industrial sectors. Our expertise ensures compliance with international standards such as ISO 14644, GMP, and FDA regulations, guaranteeing a controlled and contamination-free environment for your critical operations.
Our philosophy is “quality above everything else”, which is why our installations comply with current international standards, providing the customer with a modern, easily managed, safe installation.
Comprehensive Clean Room Solutions:
We have categorized our cleanroom system as follows:
- Architecture (Design & Engineering)
- Air Treatment
- Associated Equipment & Technology
- Validation & Compliance
- Consumables & Maintenance
- Control & Monitoring
Architecture (Design & Engineering):
Layout design is fundamental to maintaining containment/sterility commitments. The laboratory interior has to be designed to be easily cleaned and sanitized, inorganic, impermeable to liquids and resistant to any chemical agents that might be employed.
The “Systems BD” architecture system includes the following characteristics:
- It is specific for clean rooms
- It is based on a modular, constructive, integrated, coordinated and self-supporting system comprising walls, ceilings, floors, windows, doors, luminaries and sanitary fittings.
- A wide range of solutions, products and materials
- Flexibility, allowing adaptation to requirements and needs
- Compliance with cGMP requirements
Air Treatment:
In “Systems BD”, we install systems that respond to the required conditions in each clean room, employing all available technological solutions in order to comply with the customer’s economic and technical requirements.
Our systems bring the following characteristics together:
- They guarantee classification, pressure, temperature and humidity in each room.
- Installations designed from the point of view of energy efficiency.
- Advanced technological solutions that improve system performance and lengthen installation useful lifetime
- Design, selection and integration of all equipment making up the system.
Associated Equipment & Technology:
Clean zones cannot be considered as isolated zones. Their operation requires constant interaction with the exterior with a continuous flow of entry and exit of personnel and materials which, under no circumstances should be allowed to compromise the established conditions.
We supply advanced clean room equipment, including:
- HEPA/ULPA filtration systems,
- Laminar flow workstations, Dispensing/Sampling Booth
- Clean room furniture and pass-through chambers
- VHP pass boxes, BIBO systems
- Air showers and contamination control devices
Clean Room Partition Walls, Doors, Window, Lights & Accessories:

Our cleanroom partition wall systems are innovative and easy to install. The system is specially designed for pharmaceutical, hospital & Biotech industrial cleanroom environments. The components include wall panel, aluminum or steel profile to seal up the panel edges, connect two pieces of panels with metal “中” shape, and via aluminum profile bottom track to fix to floor, the entire inner and outer corner to cover with coving. Even the 3-way inner and outer connector is special die casting to flush with wall, ceiling and floor. end and corner vertical profile is also flush with wall, ceiling and floor, door and window to perfect wall systems. The whole system finishing surface will be flush, airtight, easy for cleaning and non-particles shedding, without protruding parts and cavities to accordance with pharmaceutical cleanroom characteristics.
Advantage:
- High-quality surface material is resistant to chemicals, attack, abrasion and scratches.
- VHP sterilization compatible material
- Panel four side extrusion seals up the panel edges to avoid contamination.
- High-quality thermal insulation core material.
- Embedded reinforcement structure as per requirements.
- Custom embedded pipeline for wiring conduit.
- Easy and fast installation wall systems.
- Flexible components can be selected for different requirements.
- Rigid systems to avoid air leakage.
- Systems come with complete door and window sets.
- All components can be flush connection.
Validation & Compliance:
Ensuring your clean room meets regulatory requirements is essential. Our services include:
- Certification and validation according to ISO & GMP standards
- Particle count testing and environmental monitoring
- HVAC performance assessment
Consumables & Maintenance:
To sustain optimal performance, we provide:
- Antistatic and sterile garments
- Clean room wipes and disinfectants
- Regular maintenance and cleaning services
Control & Monitoring:
All “Systems BD” installations are fitted with a robust, scalable system that permits all plant equipment and installations to be under full control.
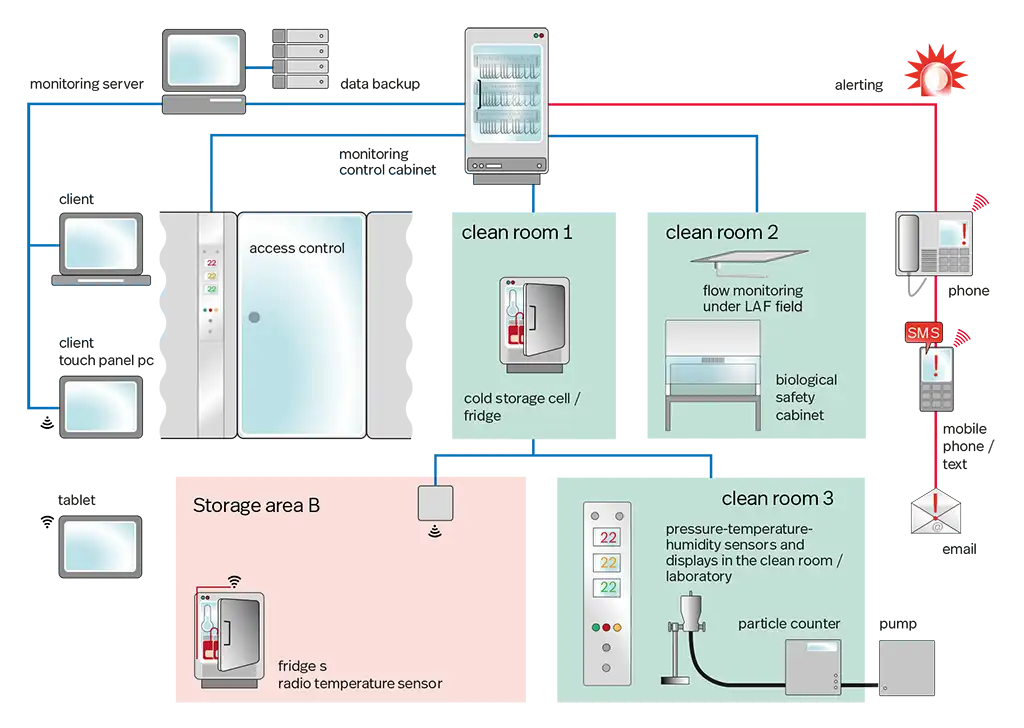
The monitoring system consists of modularly combinable components:
- Sensors for different parameters (room pressure, room temperature, room humidity, particles, flow rate, device temperatures etc.)
- Airlock / door monitoring
- On-site visualization in the clean room (digital displays, touch panels, alarm lights)
- Alarm forwarding (phone, email, text message)
Industries We Serve:
We deliver clean room solutions to various industries, including:
- Pharmaceuticals & Biotechnology – Sterile production environments for drug manufacturing and research
- Medical Devices – Contamination-free zones for the production of high-precision medical equipment
- Electronics & Semiconductor – Particle-controlled environments for microchip and semiconductor fabrication
- Food & Beverage – Hygiene-controlled spaces for food processing and packaging
Why Choose Us?
- Expertise & Experience – Decades of industry knowledge in clean room technology
- Regulatory Compliance – Solutions that meet global standards
- Turnkey Solutions – From design to maintenance, we handle it all
- Reliable Support – Dedicated technical assistance and after-sales service
Contact Us Today
Partner with us to create a world-class clean room facility that enhances your operational efficiency and compliance. Get in touch with our experts for a consultation today!