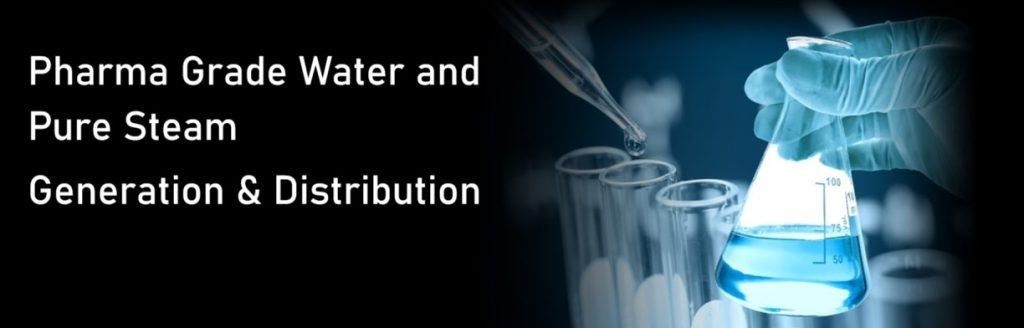
Overview
Pharmaceutical manufacturing requires the highest level of water purity to ensure product quality, patient safety, and compliance with stringent regulatory standards. Our Pharmaceutical Water Treatment Plant solutions are designed to meet international Pharmacopoeial standards such as USP, EP, and JP.
Water plays an irreplaceable role in pharmaceutical production. As one of the few raw materials produced directly on-site, it is subject to strict quality requirements and regulations.
Our aim is not only to offer technologically leading solutions but also to fulfill the highest quality and safety requirements.
We focus on the specific design requirements for water treatment plants as well as the strict requirements for their implementation and operation in order to ensure microbiological purity in production at any time.
Our Solutions
We offer a complete range of water treatment solutions, customized to the specific needs of pharmaceutical production facilities:
- Purified Water (PW) Generation
- Water for Injection (WFI) Generation
- Pure Steam Generation (PSG)
- Storage & Distribution
- Monitoring & Control Systems
Purified Water (PW) Generation:
Overview
Purified Water (PW) is a critical utility in pharmaceutical manufacturing, used in the production of oral and topical formulations, non-parenteral drug products, and cleaning processes. Our Pharmaceutical Purified Water (PW) Systems are designed to meet stringent international standards, ensuring high-purity water that complies with USP, EP, and JP guidelines.
Our PW System Solutions
We offer custom-engineered solutions to ensure compliance, efficiency, and reliability in pharmaceutical water production.
Key Features:
- Pre-Treatment: Multi-stage filtration and softening to remove suspended solids, chlorine, and hardness.
- Reverse Osmosis (RO): High-efficiency membranes to remove dissolved ions, organics, and microorganisms.
- Electrodeionization (EDI): Continuous deionization ensures consistently low conductivity and TOC levels.
- Sanitization: Thermal or chemical sanitization options for microbial control.
- Skid-Mounted Systems: Compact, pre-validated modules for fast installation and easy maintenance.
Technologies We Offer:
- Dual-pass RO + EDI systems
- Hot water sanitizable designs
- PLC/SCADA-based automated control and monitoring
- Compliance with cGMP, FDA, and GAMP standards
Applications:
- Oral solid dosage manufacturing
- Aseptic preparation areas
- Cleaning of equipment and vessels
- Utility water for cleanroom environments
Water for Injection (WFI) System:
Overview
Water for Injection (WFI) is a critical component in pharmaceutical and biotechnology industries, used for parenteral drug manufacturing, sterile product formulation, and cleaning of process equipment. Our Water for Injection (WFI) Systems are engineered to produce ultra-pure water that meets the stringent requirements of USP, EP, JP, and other international pharmacopoeias.
Our WFI System Solution:
FINN-AQUATM T-series Multiple-Effect Water Stills for Pharmaceutical Manufacturing
Powered by STERIS | Delivered by Systems BD
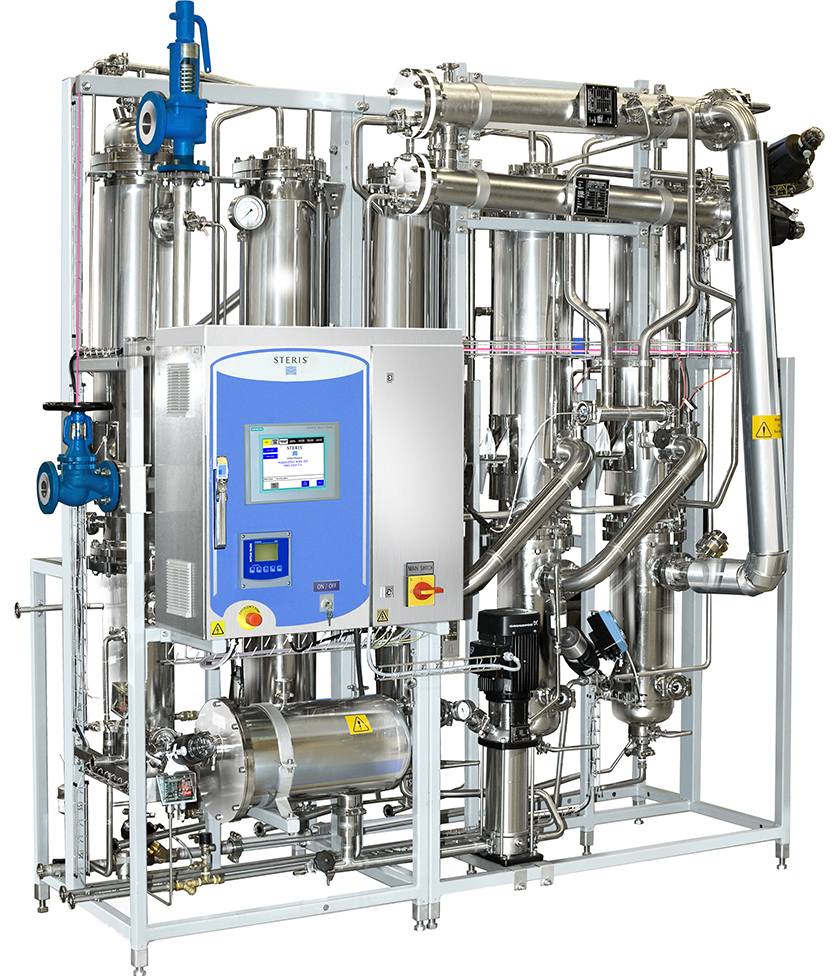
✅ Trusted WFI Solutions from a Global Leader
As an official distributor of STERIS, we provide advanced, reliable, and validated Water for Injection (WFI) generation systems tailored for the pharmaceutical, biotech, and life sciences industries.
🔬 About STERIS WFI System
STERIS is a globally recognized leader in clean utility systems. Their WFI generation systems are engineered for maximum purity, energy efficiency, and regulatory compliance.
The FINN-AQUA Multiple-Effect Water Still produces distillate that meets U.S. Pharmacopeia (USP), European Pharmacopeia (EP) and Japanese Pharmacopeia (JP) for Water-for-Injection (WFI) guidelines. The FINNAQUA Multiple-Effect Water Still is equipped with a range of features to ensure that your installation and qualification is quick and trouble-free, and that your WFI production remains efficient and reliable throughout your unit’s life. The STERIS FINN-AQUA Multiple-Effect Water Still combines optimum performance with reliable operation, reduced utility consumption and a minimal need for maintenance.
The FINN-AQUA Multiple-Effect Water Still’s design, manufacturing and performance is in
accordance with many global requirements and guidelines, including:
• ISO 9001
• ISO 14001
• OHSAS 18001
Why Finn-Aqua T-Series Multiple-Effect Water Stills?
- Cost Savings – Patented column design helps lower energy consumption.
- Easy to Maintain – Latest PLC controls and commercially available components enable lower maintenance costs.
- Highest WFI Quality – Patented three stage pyrogen separation and continuous blowdown removal from each distillation column.
- Productivity – Proportional capacity control minimizes starts/stops.
- Easy to Validate – Units are fully tested and pre-validated to customer specifications during factory qualification.
⚙️ Technical Features
- High-quality electropolished SS316L construction
- Automatic operation via PLC/SCADA
- Built-in CIP/SIP capabilities
- Minimal endotoxin and microbial load
- Optimized for energy & water efficiency
📋 Regulatory Compliance
- cGMP, EU GMP Annex 1, USP <1231>
- Fully documented DQ/IQ/OQ/PQ
- ASME BPE, ISPE Baseline Guides
🌍 Applications
- Sterile injectables
- Biotech production
- Cleanroom and formulation areas
- Critical cleaning & rinsing processes
🤝 Why Partner with Us?
- Official STERIS distributor
- In-house engineering and validation support
- Local service & spare parts availability
- Turnkey project execution: Design to Commissioning
Pure Steam Generation (PSG) & Distribution:
🔹 Pure Steam Generation (PSG) Solutions – Powered by STERIS Corporation, USA.
As the trusted distributor of STERIS Corporation, we deliver industry-leading Pure Steam Generation systems tailored for the pharmaceutical, biotech, and healthcare industries.
Pure Steam is essential for sterilization and cleanroom humidification in regulated industries. Produced by heating purified water, pure steam must meet stringent standards such as EN285 and HTM 2031. Our PSG systems, manufactured by STERIS, guarantee consistently high-quality steam free from endotoxins and non-condensable gases.
Why Choose STERIS Pure Steam Generators?
- 🔧 Electropolished 316L SS Construction
Patented three stage pyrogen separation and continuous blowdown removal process ensures durability and high purity levels.
- 📈 Consistent Steam Quality
Meets global pharmacopeia and cGMP standards. - 🔍 Automatic Blowdown & Drain
Reduces scaling and improves efficiency. - 💡 PLC-Based Control System
Enables precise monitoring and integration with SCADA. - Cost Savings – Patented column design helps lower energy and utility consumption.
Productivity – Tight pressure control and quick response time shortens sterilization cycles.
- 🧪 Validated Performance
Units are fully tested and pre-validated to customer specifications during factory qualification..
Industries & Applications:
- 💉 Pharmaceutical Manufacturing
- 🧬 Biotech Facilities
- 🏥 Hospitals & Cleanrooms
- 🚿 SIP (Sterilization-In-Place) Systems
- 🌫️ Cleanroom Humidification
Documentation & Compliance
- cGMP & GAMP 5 Compliant
- 9001
- ISO 14001
- OHSAS 18001
- ASME BPE Design Standards
- FAT/SAT & IQ/OQ Documentation Provided
- 3.1 Material Certification
Pure steam distribution:
The pure steam distribution must be designed so that the least quantity of condensate enters the sterilized equipment. Components in contact with clean steam must have the same characteristics with respect to materials and surface finish as the water distribution loops. This distribution must be well insulated to minimize heat losses and the production of condensate and also to achieve energy savings in the system.
The main items of the clean steam network are:
Piping
Fittings (Elbows, Tees…)
Point of use Valves
Steam Traps